Digital printing technology is the product of the combination of digital technology and traditional printing and dyeing technology, and it is a revolutionary breakthrough in the traditional printing and dyeing industry. In the context of digitalization and networking, digital printing represents the technological development direction of the printing and dyeing industry in the future. It has been about ten years since the digital printing of fabrics in my country was recognized and applied. The industry insiders have reached a lot of consensus on its superiority, and it is called "a revolution in fabric printing technology" or "universal printing technology". ". Therefore, the industry has placed high expectations on this technology. In recent years, the progress of fabric digital printing has not been satisfactory. Although the number of models, printing materials and practitioners are increasing, most of the fabric digital printing products are still in transfer printing, and there are few direct Spray on fabrics. The progress of digital printing of fabrics can be explained from three factors: printing system, digital printing machine and printing material.
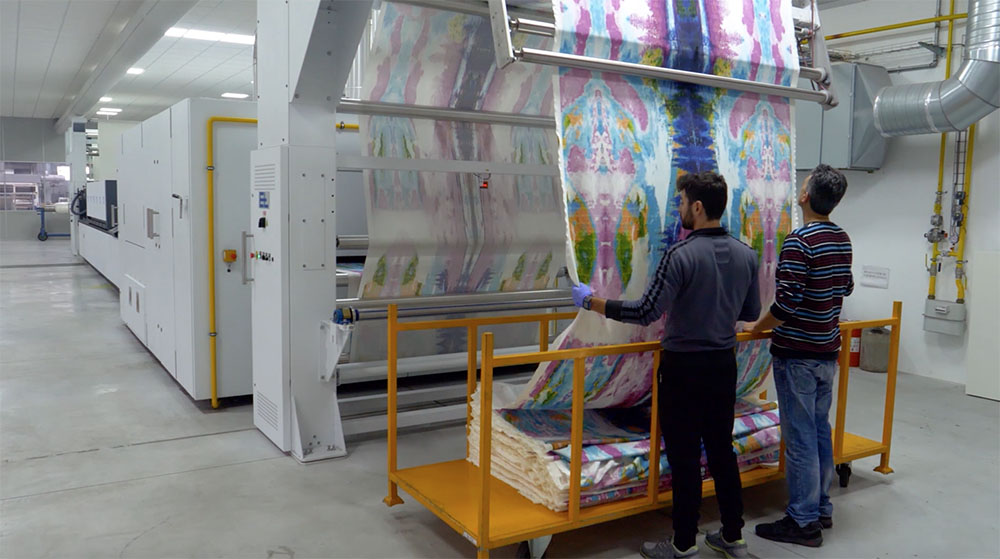
1.1 Digital printing system
Digital printing of fabrics began in the 1970s with the aim of developing a non-contact printing system that digitally produces multi-color patterns. Rapid progress was made in the 1990s, completing the transition from technical models to production applications. At the 1999 Paris International Textile Machinery Exhibition, the digital inkjet printing system received widespread attention in the industry. At that time, most of the designed production systems had low resolution and were only used for the printing of carpets and pile up furniture, and the dyes used for printing had to be specially screened, which limited the application of this technology.
The Millitron system of Milliken Company in the United States and the ChromoJet system of Zimmer Company in Austria used the principle of solenoid valve at the beginning, and used the computer to control the ink jet and air jet to print the desired pattern according to the pattern requirements. At that time, the printing accuracy (resolution) was not high, only about 20dpi, and the height was only 40dpi. It was not suitable for printing work clothes and other fabrics, but only for carpet printing. In the 1980s and 1990s, due to the improvement and improvement of nozzle manufacturing technology, the use of heated bubbles and piezoelectric nozzles, which improved the fineness of printing, set off a wave of research on digital printing. For example, Japan's Seiren company engaged in the research of CAD piezoelectric inkjet printing technology in 1987, developed the Viscotecs system, and began to put into mass production in 1990; Japan's Zhongfang and Canon developed a "singular printing" system (bubble type) in 1993; Around the same time, Japan's Konica and Sumitomo developed inkjet printing equipment such as the Nassenger system (piezoelectric).
Due to the continuous advancement of computer technology, it is now possible to automatically read out the original pattern (or digital photography software that scans or directly enters the pattern) through the computer, and after digital processing, inkjet printing directly on the fabric, that is, inkjet printing for digital fabrics printing technique. It is said that the Viscotecs system of Japan's Seiren Company produced 10 million square meters of fabrics in 1998, with sales of 12 billion yen. All kinds of fibers such as cotton, wool, silk, polyester, nylon and elastic fibers are available; woven, knitted, raised, artificial fur, etc. are complete, and the finished products have a wide range of applications. Now Ruyi, Belgium, Germany, the Netherlands, France, the United States and other countries are making progress.
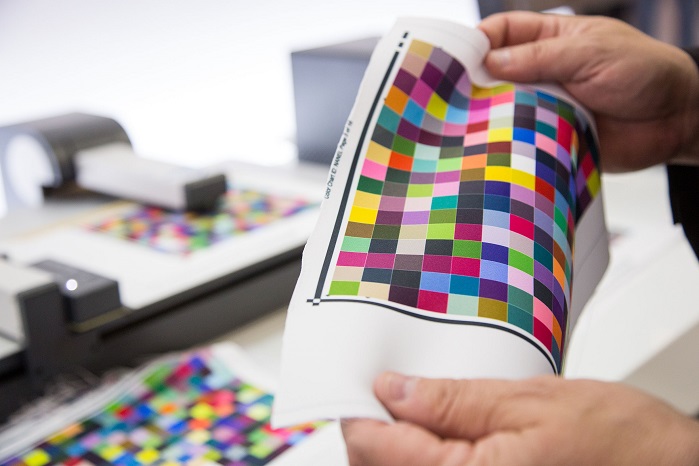
1.2 Digital printing machine
The models of fabric digital printing machines have not been perfected. The fabric digital printing machines come from inkjet printers or inkjet printers in the printing industry. At present, there are many manufacturers of such equipment at home and abroad, with hundreds of models, but they are specially designed. There are not many inkjet machines for fabric printing. The Dutch company Stork first launched the Amber digital printing machine in 1999. After improvement, it can use acid dyes for real silk and nylon/elastic silk printing, as well as pigment printing or disperse dye transfer printing, so that the machine can be used in any High-quality printing on an unbleached cotton fabric without pre- and post-processing (except for pigment-printed heat-fixing). In addition, Stork also introduced Zir-con polyester printing machine and Amethyst printing machine, which are suitable for high-volume in-and-out printing, which can be used for proofing and small batch production. It is especially suitable for printing factory trial products and mass customized product production. The Amethyst printing machine can print on cotton, silk and viscose and other natural color cotton fabrics. It adopts 8-color continuous inkjet technology, which can carry out photographic true color printing or full proofing that can accurately reflect the color and quality of batch printing; CAD files, Scanned images or digital photos are directly input into the machine, and printed on natural cotton cloth with a maximum effective width of 1650mm. The daily printing output can reach 350m, the installed cloth roll can reach 250m, and the ink storage capacity can provide 16 hours of uninterrupted printing. Amethyst uses the Windows platform Stork/Lectra software and is compatible with Stork, Lectra and various other CAD design software packages.
In China, Hangzhou Honghua Digital Co., Ltd. began to research and develop inkjet printing technology for digital fabrics around 1997, and it has progressed rapidly. In July 2000, it was appraised by the former State General Administration of Fabrics and Zhejiang Provincial Department of Science and Technology. The technology is at the international advanced level. Except for some imported nozzles, its piezoelectric printing equipment and computer software are all designed and manufactured by itself.
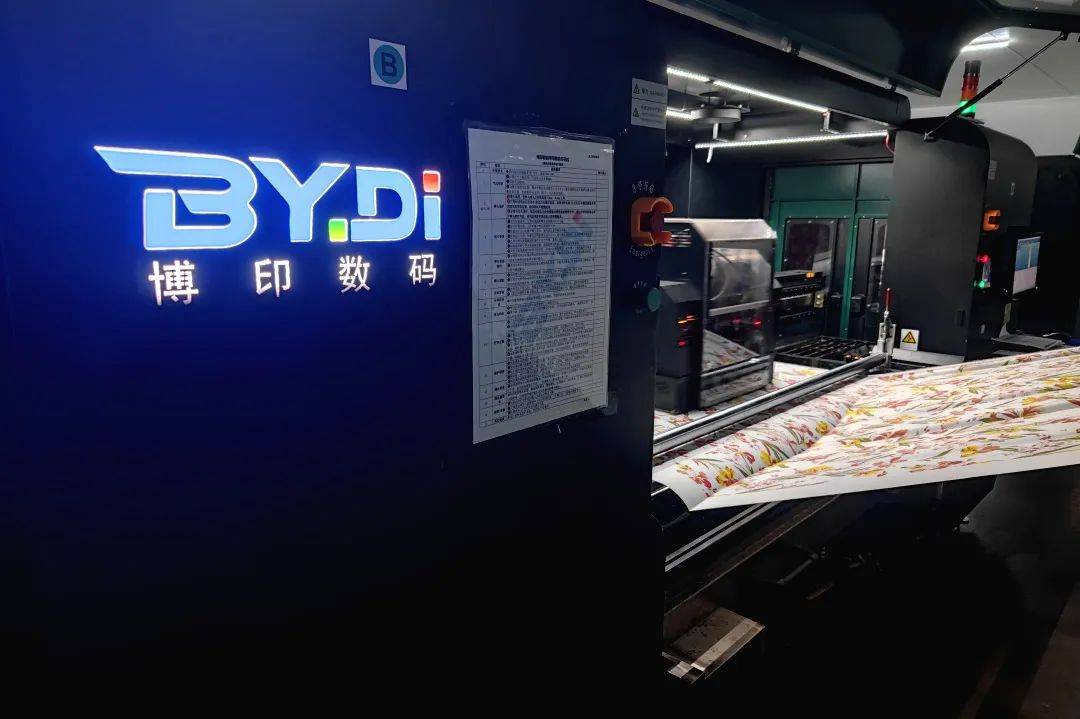
1.3 Printing materials
Printing material is the core equipment for digital printing of fabrics. At the beginning, the three kinds of inks (ie reactive dyes, acid dyes and disperse dyes) proposed by Swiss company Ciba have been developed in China since the late 1990s. Disperse dye particles are easy to block the print head of the printing machine, and the pigment ink has many requirements on the quality of the adhesive; in addition, the temperature conditions of the same color post-treatment, various dyeing fastness and softness are the main contents to evaluate them. From today's perspective and information, there are many brands of ink, and manufacturers are promoting their products, but none of them have been well received in practical applications. We understand that a dye (pigment) ink system (4 colors, 6 colors, 8 colors) has a color matching software in the printing process. This software has specific specialties and is applied to different machine models. Therefore, each ink manufacturer must provide color matching software when launching its own ink. This is a relatively complex and difficult system engineering, which has a greater impact on the color level, vividness, fullness and other qualities of printed products.
At present, the companies and corresponding products that are relatively good in digital printing printing materials include: CibaAlcoprintCT-D, the printing paste of Ciba Specialty Chemicals of Switzerland; BalixanP100HS series dyes of BASF company of Germany; J-Teck3 company of Italy The disperse dye ink J-EcoPrint that can directly print fabrics (very suitable for today's piezoelectric inkjet printing machines); Italy For. A new series of pigment inks GenestaPG supplied by rex, which consists of 9 colors; KonicaMinoda of Japan has added a series of reactive dye inks; Sawgrass of the United States has launched the first direct dye ink for cotton, and Italian machinery manufacturer MacchineeServizi (MS) has collaborated to produce the NaturaLink series of inks for use in the MS-One digital garment printing machine.
Post time: 09-01-2022